A Strong Case for Grinding With Hybrid
Metal-Bond Wheels
As seen in Cutting Tool Engineering
by Alan Richter, Editor
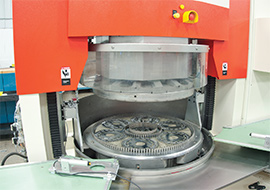
One of two Stahli DLM 705 double-disc grinders Aggressive Grinding Service uses to grind carbide discs with ATI’s hybrid metal-bond, induced-porosity wheels.
Since its founding in 1988, Aggressive Grinding Service Inc. has committed itself to continuous improvement to satisfy its mission of quickly delivering high-quality carbide and ceramic parts, according to President/CEO Lester Sutton. As part of that improvement process, the Latrobe, Pa.- based company recently began testing and evaluating hybrid metal-bond, induced porosity grinding wheels from Abrasive Technology Inc.
“While certainly not a stranger to this type of bond in other departments, we made the switch in our surface grinding department, specifically on our double-disc grinders,” said Engineering and Quality Manager Randy Lechner.
The shop has two Stahli DLM 705 double-disc grinders, both with a 28″ wheel diameter and six-carrier arrangement. Sutton explained that a double-disc grinder simultaneously grinds the top and bottom of workpieces. Workpieces are held in a round fixture, which rotates with a drive ring in the center of the machine, so the parts are moving in a circle from inside to outside and around the grinding wheels. “It’s kind of like a Spirograph,” he said. “We find, in many cases, double-disc grinding is from 10 to 30 times faster than surface grinding.”
According to Lechner, Aggressive Grinding Service grinds 2″-dia. carbide discs, with six carriers holding three parts for a total of 18 per load. The coolant is SintoGrind TTS-US synthetic cutting oil, applied at 40 psi and cleaned with a One Micron filtration system from Transor Filter.
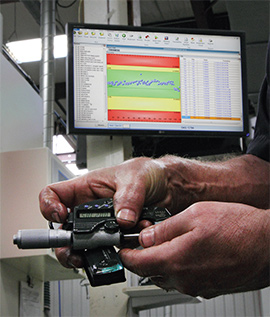
Wireless digital micrometers send a realtime data point signal, captured by the MeasurLink® system, to the SPC database which is then displayed on overhead screens posted throughout the shop.
The company removes 0.040″ from the workpieces. It previously applied ATI pie-segment, resin-bond wheels with the following parameters:
- 15-minute cycle time
- 0.0027-ipm feed rate;
- 0.153-cu.-in./min. mrr;
- 325 rpm for the top and bottom wheels
- 20 rpm for the center ring
- Pressure of 400 to 900 lbs (controlled by the feed rate)
In this operation, wheel dressing took place once every 234 parts.
After switching to ATI pie-segment, hybrid metal-bond, induced-porosity wheels, the shop achieved the following:
- 12-minute cycle time
- 0.0034-ipm feed rate
- 0.192-cu.-in./min. mrr;
- 325 rpm for the top and bottom wheels
- 20 rpm for the center ring
- Pressure of 250 to 600 lbs (controlled by the feed rate)
In this operation, wheel dressing takes place only at the end of the 600-part order.
The induced porosity of this bond allows for a cooler, more free-cutting action,” Lechner said. “The wheel has shown a 50 percent increase in life as a function of material removed and the number of parts ground between wheel dressings.” Dressing is done with a circular, 150-grit, Al2O3 stone.
He noted, however, that the resinbond wheels impart a surface finish of 8 to 10 μin. Ra while the finish is 16 to 20 μin. Ra for the hybrid metal-bond ones. “Overall, we feel this metal-bond wheel is more cost-efficient based on stock removal vs. wheel life alone,” Lechner said, adding that reduced cycle time and dressing frequency are added benefits.
“It’s probably as significant of an improvement as I’ve seen in my 30 years of grinding,” Sutton said.
Aggressive Grinding Service, discusses important parameters for the grinding of advanced ceramic materials.
Download PDF
Download MP3
View the article
Listen to the full interview below.
The cover photo of August's Ceramic Industry features our wireless digital micrometers that send a real-time data point signal, captured by the MeasurLink® system, to the SPC database which is then displayed on overhead screens posted throughout the shop.